技術情報・技術コラム
超硬合金の進化の歴史を基礎から解説!
超硬素材の選定・開発から超硬加工のことならエバーロイへご相談ください
超硬合金はダイヤモンドに次ぐ硬さを誇り、耐摩耗性や抗折力(曲げ強さ)、剛性、耐衝撃性などにも優れており、切削工具や金型として活用されており、自動車や航空機などの精密機械、建設機械など、さまざまな業界でなくてはならない存在です。
超硬合金は、2024年現在から約100年前に生み出され、それまでよりも遥かに早く簡単に硬い材料を加工できるようになり、ドリルなどの切削工具に革命を起こしました。どのような進化を辿ってきたのか、誕生から現在までの歴史を解説します。
超硬合金とは?
超硬合金とは、タングステンカーバイド(WC)などの硬質金属炭化物と、コバルト(Co)などの金属を焼き結んで製造される金属です。高い硬度や耐摩耗性、耐衝撃性、剛性、耐熱性などを誇り、幅広い使用環境にも耐え得る素材です。
その硬さはダイヤモンドに次ぐほどで、高い硬度が要求される切削工具や金型などに幅広く活用されており、汎用性の高い材料として知られています。高い耐摩耗性のおかげで、長寿命なのも魅力の一つです。
切削工具用の超硬合金材種は、P種・M種・K種の3種類に大別され、それぞれ特徴が異なるため以下のように作業用途が異なります。
分類 |
特徴 |
適応被削材 |
---|---|---|
P種 |
炭化チタンや炭化タンタルなどを多く含み、耐熱性・耐溶着性に優れる |
● 鋼 ● 合金鋼 ● ステンレス |
M種 |
炭化チタンやタンタルを適度に含み、熱的・機械的損傷に強い |
● ステンレス ● 鋳鉄 ● ダクタイル鋳鉄 |
K種 |
タングステンカーバイド主体の合金で強度に優れ、特にすきとり摩耗など機械的損傷に強い |
● 鋳鉄 ● 非鉄金属 ● 非金属 |
ただし、主な原料であるタングステンがレアメタルなことや、高い硬度のため加工が難しいことなどから、ダイス鋼やハイス鋼と比べると高価で、イニシャルコストは高くなっています。
関連記事:超硬合金とは?特徴や種類について解説!
超硬合金の歴史
超硬合金の歴史は、1923年にドイツのK. Schroterが開発したのが始まりです。ドイツでは第一次世界大戦後にアフリカからのダイヤモンドが入手できなくなったことで、代用品として開発が進められました。
開発から3年後の1926年には「ウィディア(ダイヤモンドのような)」と名付けられ、鉄鋼メーカーのクルップ社から発売されました。その後アメリカや日本でも商品化・研究が進められていきます。
当初は、タングステンと炭素の粉末を水素雰囲気で炭化してタングステンカーバイドを作り、コバルト粉末を加えて焼結するもので、現在の超硬合金よりも脆い材料でした。鋼の切削には適さず、主に鋳鉄・黄銅の加工に使用されていました。
その後、鋼の切削には鉄と反応しにくい、炭化チタン・炭化タンタル・炭化ニオブなどを添加すると適した合金が作成できると判明し、1931年にはクルップ社から発売されます。現在、工具として使用される超硬合金の基礎が確立されました。
現在に至るまでも超硬合金の改良は続いており、切削や耐摩耗、耐衝撃、鉱山用工具など幅広い分野で活用されています。近年では超硬合金の表面に、化学蒸着(CVD)法や物理蒸着(PVD)法により、硬質膜を被覆する手法が開発され、表面にコーティングを施すことでさらに機能を付加した被覆専用超硬合金も使用されています。
超硬合金は、工業製品の進化・発展とともに改良され続けており、ボタン一つで複雑な超硬工具が作れる時代になってきました。ただし最新鋭の機械でもできない加工は多く、熟練した職人による加工技術力も必要不可欠です。
日本での超硬合金の歴史
日本での超硬合金の歴史は、1929年に東芝の前身である「芝浦製作所」と「東京電気」が超硬合金「タンガロイ」を開発したことから始まります。1926年の「ウィディア」発売から2年後の1928年頃から東芝・住友電気工業・三菱金属各社で独自に研究が開始されており、1年足らずで完成させました。
また三菱マテリアルの前身である三菱鉱業の「トリディア」や、住友電工ハードメタルの前身である住友電気工業の「井ゲタロイ」など、次々に超硬合金の開発・発売が進められました。
これらの企業がリーディングカンパニーとして国産超硬合金の開発を推し進めていき、現在では超硬合金による金属精密加工がなくてはならないものとなっています。
切削工具メーカーが日本で発展した背景
日本では超硬合金の研究開発がいち早く行われ、切削工具メーカーが発展していきました。大きく発展を遂げることができた背景には、下記3つの影響があります。
- 軍需景気
- 機械工具販売店の存在
- ハイスと超硬合金の開発
軍需景気
切削工具メーカーが日本で発展した背景として、軍需景気が挙げられます。当初は輸入品に頼らざるを得なかった切削工具産業でしたが、日露戦争を機に機械工業や工具の重要性が認識されるようになり、国産化への機運が高まっていきました。
初期の国産切削工具は、輸入品の模倣から始まり、着実に技術力を蓄積していきます。満州事変や太平洋戦争が勃発すると、航空機や兵器といった軍需品が大量生産されるようになり、生産が追い付かないほどに需要が拡大します。
しかし当時は超硬合金が普及しきっておらず、ユーザーは超硬工具を十分に活用できませんでした。また設備機械の性能も不十分だったこともあり、軍からの依頼により現在のタンガロイ・住友電工・三菱マテリアルの3社が、各地の軍需工場の技術指導にあたりました。
超硬合金の分野では後発であった日本ですが、軍需産業の発展により切削工具の国産化と技術力アップが進み今に至ります。
機械工具販売店の存在
日本の切削工具メーカーの成長には、機械工具販売店の存在も大きな役割を果たしてきました。機械工具販売店の歴史は、切削工具メーカーよりも古く、幕末にオランダから機械・工具の輸入を行ったのが始まりです。イギリス・フランス・ドイツなどのヨーロッパ製品を取り扱っていくようになり、成長していきました。
時代が進み第一次世界大戦中に、工具の輸入が難しくなると、国内の切削工具メーカーが台頭し始め、次第に機械工具販売店も国産工具を取り扱うようになっていきます。軍需景気による切削工具メーカーの躍進は、機械工具販売店による国産工具の販路拡大も欠かせない要因だといえます。
ハイスと超硬合金の開発
切削工具メーカーの発展には、ハイスと超硬合金の国産開発も関係しています。ハイス工具の国産化に向けた取り組みは1907年頃から始まっており、それから70年あまりは切削工具にはハイスが用いられるのが主流でした。
1926年に超硬合金がドイツで誕生すると、日本の切削工具メーカーもほぼ同時期に次々と超硬工具の事業を開始しており、前述の通り1929年には国産の超硬合金「タンガロイ」が開発されています。
このように日本では、切削工具に欠かせない「ハイス」「超硬合金」どちらとも早くから国産化に取り組んでおり、高品質な切削工具を量産する技術を確立してきました。積極的に国産化に取り組んだことや長年の技術の蓄積が、世界に通用する切削工具メーカーへ発展する土台となっています。
現在でも超硬工具は進化を続けており、新工具形状の開発やコーティング技術の進化など、革新され続けています。
超硬合金の特徴
超硬合金の特徴は、大きく3つあります。
- 硬度・耐摩耗性・耐久性がある
- 圧縮強度が高い
- 高荷重・高温にも耐える
それぞれ解説していくので、どのような特徴があるのか押さえておきましょう。
硬度・耐摩耗性・耐久性がある
超硬合金はダイヤモンドに次ぐ高い硬度を誇り、高水準の耐摩耗性・耐久性も持ち合わせています。金属を加工する切削工具や金型に使用しても、加工対象の金属(鉄やステンレスなど)より硬度が高いため、傷や摩耗に強く精密な加工を施せます。
変形しにくいことから、工具・金型の寿命が長く長期間使用し続けられるため、コストパフォーマンスに優れるのも魅力です。
また、温度の変化によって硬さが変化しないのもメリットです。金属によっては特殊な条件で硬さが変化するものもありますが、超硬合金は常温でも高温でも硬度が変化しません。摩擦熱などで高温になる切削工具に使用しても、常に同じクオリティで仕上げられます。
圧縮強度が高い
硬度だけでなく、圧縮強度が高いのも超硬合金の特徴です。圧縮強度とは、どれだけ外部からの圧力に耐えられるかの指標で、値が高いほど圧力を受けても変形しにくいことを表します。
超硬合金は金属の中でも高い圧縮強度を誇るため、工具や金型として使用する際に高い圧力がかかっても、破損・変形することなく形状を保ち続けられます。例えば自動車産業など、精密な部品作りが必要な多彩な工業分野で、重宝される信頼性の高い材料です。
高荷重・高温にも耐える
高荷重・高温に耐えられるのも特徴で、同じ重みを加えても鋼より変形しにくく、高荷重環境でも高い精度を維持し続けられます。長期間にわたり安定した作業が可能です。
また、高荷重・高温の環境でも変態しないことも、超硬合金の大きな特徴です。金属における変態とは、金属の状態が何らかの原因で変化する現象のことを指します。例えば鉄は加熱していくと、一定の温度で原子配列が変わり、性質ががらっと変わってしまいます。
超硬合金の場合は加熱・冷却を何度繰り返しても、変質しない安定した合金です。どのような環境でも使用しやすくなっています。
超硬合金の加工特性
超硬合金は高い硬度や耐摩耗性などから、硬い素材を加工するのに適しています。ただし超硬合金の加工にはダイヤモンド砥石や放電加工が必要となり、専門設備や高硬度素材の加工ノウハウ・技術が必要です。
また、硬度は高いものの衝撃強度や靱性(粘り強さ)は低くなっており、欠けやすい・割れやすい特性があります。加工時に衝撃を受けると、破損やチッピングが生じやすくなっています。
超硬合金の製造過程で添加される素材元素によって、特性に差が生じるため、使用目的や製造時に使用する金属などの性質に合わせて、適した超硬合金を選ぶことが大切です。
超硬合金の主な用途
超硬合金は硬く変形しにくく、恒温下でも硬度が下がりにくいため、耐摩耗性が要求される加工に使用されます。
例えばNC旋盤やマシニングセンターに使用される金属加工用の切削工具の刃先や、プレス金型などに使用されるのが一般的です。
使用される業界は多岐にわたり、自動車・建設機械のエンジンや減速機、航空機のエンジン・機体、発電機、掘削機器、電子機器など、多方面で活躍しています。
まとめ
超合金の歴史は1900年代初頭のドイツから始まり、時代の変化に応じて発展してきました。現在では多様な分野で活用されており、製造方法の違いにより多彩な特性を持つ超硬合金が生み出されています。
一口に超硬合金といっても種類によって特徴が異なるため、活用したい環境や加工したいものなどに応じて、最適な種類を選択する必要があります。
「超硬素材・超硬加工 ソリューションナビ」は、最適な超硬素材の選定・開発から加工、完成品の提供まで一貫して提供しており、多くの企業から選ばれ続けてきました。無料でご相談を受け付けているので、まずは気軽にお問い合わせください。
超硬素材の選定・開発から超硬加工のことならエバーロイへご相談ください
この記事を監修した人
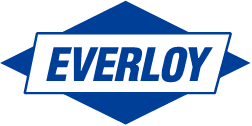
大久保 文正
エバーロイ商事株式会社
昭和33年の設立以来、長年にわたり超硬工具の販売。
その製品はエバーロイの名で、広く多くのお客様からご支持をいただいております。
技術革新の激しい時代の中、お客様のあらゆるニーズに対応すべく、製販一体となって当社のオリジナリティを生かした営業活動を推進して参ります。
超硬素材・超硬加工 ソリューションナビを運営するエバーロイは、
素材選定・開発~精密加工、完成品提供までの一貫したソリューション提供により、
皆さまの課題を解決します。
-
技術資料ダウンロード
これまで培ってきた実績・ノウハウをもって
資料ダウンロードフォーム
皆様に高付加価値な超硬を提供いたします。 -
お見積もり•お問い合わせ
06-6452-2271お問い合わせフォーム -
よくある質問
過去お客様より多くのお問い合わせ いただいた内容を掲載しています。
詳しくはこちら